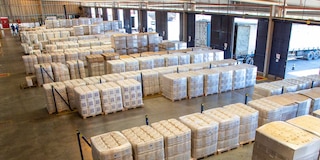
De optimale voorraad van uw magazijn berekenen
Het aanhouden van een optimale voorraad in een magazijn, is essentieel voor een efficiënte logistiek en om extra kosten in het opslagproces te vermijden. Hoeveel voorraad is er nodig om aan de vraag naar een product te voldoen en tegelijk een voorraadtekort te voorkomen?
In dit artikel wordt dieper ingegaan op de optimale voorraad in de logistiek, en worden de verschillen besproken tussen dit concept en de begrippen minimale voorraad en veiligheidsvoorraad. Bovendien ontcijferen wij de formule om een voorraadniveau te bereiken dat in overeenstemming is met de vraag, de installatie en de geleidelijke groei van uw bedrijf.
De optimale voorraad: definitie en toepassingen
In de logistiek verwijst de optimale voorraad naar de exacte hoeveelheid, die een bedrijf nodig heeft om aan de gebruikelijke vraag te voldoen zonder met een tekort te maken te krijgen. Met andere woorden, het doel is een optimale rentabiliteit te bereiken en de opslagkosten tot een minimum te beperken.
Dit begrip moet niet worden verward met de gemiddelde voorraad, die wordt berekend door het gemiddelde te nemen van de voorraden in het magazijn. Deze waarde ligt tussen de maximum voorraad, dit is de totale hoeveelheid artikelen die in de faciliteit kan worden opgeslagen, rekening houdend met de totale oppervlakte en de opslagoplossingen, en de minimale voorraad, die het bestelpunt vormt voor het aanvullen van de voorraad.
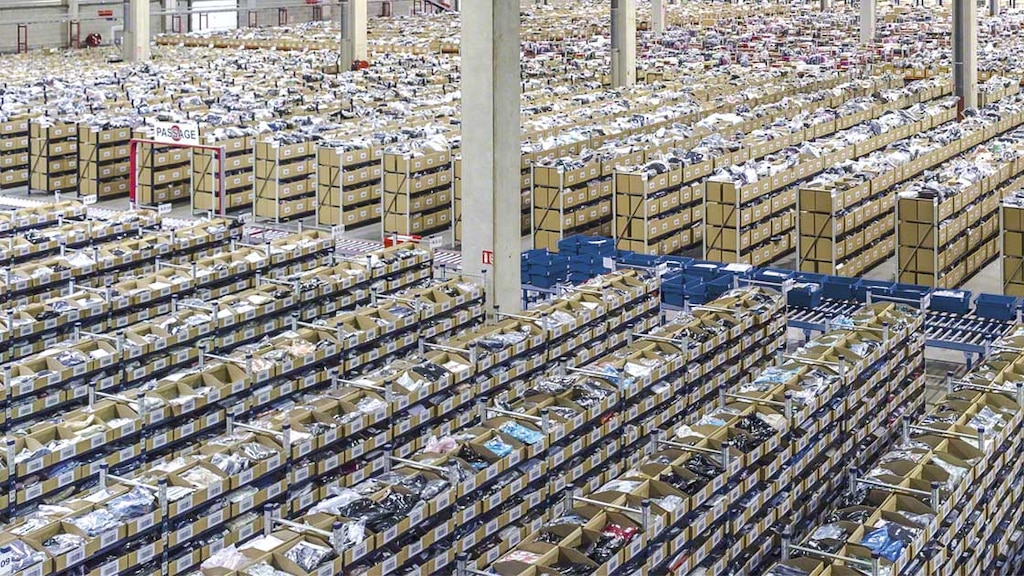
Hoe wordt de optimale voorraad berekend?
Met welke elementen moet de magazijnmanager rekening houden om de optimale voorraad te berekenen? Hoewel dit afhangt van de strategie van elke onderneming, zijn de volgende vier elementen van belang:
- De klantvraag: de logistiek manager moet, in samenwerking met de boekhouding en de directie, de evolutie van de vraag in de loop der jaren analyseren, alsmede de prognose van de vraag naar elke referentie, en de seizoengebondenheid van elk product.
- De omloopsnelheid van de voorraden: de magazijnmanager moet op de hoogte zijn van de omloopsnelheid van elke referentie om de opslaglocatie van de goederen correct te kunnen beheren. De ABC-methode is een gangbaar criterium voor het organiseren van de voorraden al naargelang het vraagniveau.
- Het producttype: de kenmerken van elk product en van uw bedrijfssector zijn van essentieel belang om de optimale voorraad voor de geïnstalleerde opslagsystemen in te kunnen schatten. De logistiek van levensmiddelen bijvoorbeeld vereist een proces met temperatuurbeheersing voor de opslag van bederfelijke goederen, en kan niet vergeleken worden met de opslag van kabels of leidingen, waarvoor speciale opslagsystemen nodig zijn die aan de specifieke kenmerken van de producten zijn aangepast.
- De maximale, de minimale en de veiligheidsvoorraad: met behulp van deze drie waarden kan de optimale voorraad voor elke SKU worden berekend. De beschikbare ruimte, de opslagoplossingen, en de apparatuur voor goederenafhandeling zullen dus bepalend zijn voor het maximale voorraadniveau. Terwijl de minimale voorraad bepaald wordt door de vraag en het vermogen om de bestellingen te verwerken. De kenmerken van het bedrijf zullen bepalen welke veiligheidsvoorraad of reservevoorraad vereist is.
- De doorlooptijd of Lead Time: de magazijnmanager moet ook de doorlooptijd of Lead Time van elke leverancier kennen, dat wil zeggen, de tijd tussen het genereren van een bestelling en de levering van het product door de leverancier.
In een logistieke omgeving waar resultaten en kostenvermindering bij de goederenopslag steeds belangrijker worden, kan het niet in aanmerking nemen van een optimale voorraad ernstige gevolgen hebben voor uw bedrijf, zoals inefficiënte opslagprocessen, dure voorraadoverschotten en vooral het verlies van opgeslagen producten, met name bederfelijke goederen.
Voorraadtypes: optimale voorraden, minimale voorraden en veiligheidsvoorraden
Het is niet mogelijk de optimale voorraad te begrijpen zonder andere concepten te begrijpen, zoals de fysieke of technische voorraad, de veiligheidsvoorraad of de minimale voorraad. De verschillende soorten voorraden, in combinatie met de logistieke strategie:
- De beschikbare voorraad: de bestaande voorraad in het magazijn die kan worden gebruikt om een bestelling samen te stellen. Alle logistieke processen worden uitgevoerd op basis van de beschikbare voorraad, ook wel fysieke of technische voorraad genoemd.
- De minimale voorraad: is de minimale hoeveelheid van elk product, die in het magazijn aanwezig moet zijn om aan de vraag te kunnen voldoen.
- De veiligheidsvoorraad: elk magazijn moet een veiligheids- of buffervoorraad aanhouden, om een voorraadtekort bij een onverwachte toename van de vraag, te voorkomen.
- Het bestelpunt: is een numerieke waarde in de logistieke strategie, die bepaald wanneer er een bestelling bij een leverancier moet worden geplaatst. Deze waarde ligt tussen de minimale voorraad en de optimale voorraad.
- De maximale voorraad: dit is het voorraadniveau dat nooit mag worden overschreden, zodat de werking van het magazijn gewaarborgd blijft. Het is gekoppeld aan de opslagcapaciteit en aan het aantal medewerkers in het bedrijf.
Zodra dit vastgesteld is, kan de optimale voorraad berekend worden die, zoals eerder vermeld, gelijk is aan de veiligheidsvoorraad die moet worden aangehouden opdat de onderneming een optimale rentabiliteit kan behalen, en tegelijkertijd zowel aan de huidige vraag als aan eventuele schommelingen daarvan kan voldoen.
De formule voor een optimale voorraad
Zodra de logistiek manager rekening heeft gehouden met de elementen in het vorige punt, moet hij de optimale voorraadformule gebruiken om te weten te komen hoeveel er van elk artikel in het magazijn aanwezig moet zijn. Dit cijfer wordt verkregen uit de optimale bestelhoeveelheid, waaraan de minimale voorraad en de veiligheidsvoorraad van het magazijn moeten worden toegevoegd. Hieronder wordt uiteengezet hoe deze variabelen kunnen worden verkregen:
De optimale bestelhoeveelheid is gerelateerd aan de formule van Camp, die tot doel heeft het voorraadbeheer en de aankoop van grondstoffen te optimaliseren, op basis van de hoeveelheid en de frequentie van de bij de leveranciers geplaatste bestellingen. Deze numerieke waarde wordt berekend aan de hand van de volgende formule:

Waarbij Q = de optimale bestelhoeveelheid (Quantity), D = de jaarlijkse vraag van het product (Demand), K = de prijs van elke bestelling, en G = de opslagkosten van een product gedurende een vastgestelde periode. Dankzij de formule van Camp, zal de magazijnmanager weten wanneer hij een bestelling moet plaatsen.
Naast de optimale bestelhoeveelheid, is het belangrijk de minimale voorraad en de veiligheidsvoorraad van het magazijn te bepalen. Formule voor het berekenen van de minimale voorraad:

Aan dit product moet de veiligheidsvoorraad worden toegevoegd, die kan worden berekend op basis van de volgende variabelen:
- De Lead Time of doorlooptijd van de toeleveranciers onder gewone omstandigheden.
- Maximale leveringstijd in geval van een incident.
- Gemiddelde vraag naar het product.

En de formule voor het berekenen van de optimale voorraad is als volgt:
Optimale voorraad = optimale bestelhoeveelheid + minimale voorraad + veiligheids- of buffervoorraad
Voorbeeld van het berekenen van de optimale voorraad
Hieronder volgen enkele voorbeelden van berekeningsformules. Het magazijn met grondstoffen van een staalbedrijf bevoorraadt de productie-eenheid met schroeven. De onderneming heeft 80.000 schroeven per jaar nodig voor de fabricage van het plaatwerk dat ze op de markt brengt.
Elke bestelling van het bedrijf geplaatst bij zijn toeleverancier van schroeven, kost € 100,-. De opslagkosten van één schroef bedragen 5 cent per jaar. Wat is de optimale voorraad schroeven voor dit bedrijf?
Zoals reeds gezegd, is de eerste stap bij de berekening van de optimale voorraad het bepalen van de optimale bestelhoeveelheid. Door de volgende formule te gebruiken, waarbij K (de kosten van een bestelling) € 100,- bedraagt, D (de jaarlijkse vraag) gelijk is aan 80.000 schroeven en G (de opslagkosten voor één schroef) € 0,05 bedraagt, dan verkrijgt men Q = 17.888 schroeven:
Q (maximaal te bestellen hoeveelheid) = √((2 x 100 x 80.000) / 0,05) = 17.888 schroeven
Om de optimale voorraad te berekenen, moet vervolgens de minimale benodigde voorraad in het magazijn worden bepaald. Hiertoe moet bepaald worden, hoeveel schroeven het bedrijf per dag nodig heeft. In het geval van 250 werkdagen per jaar, heeft de onderneming 320 eenheden per dag nodig. Indien de doorlooptijd van de leverancier precies een week bedraagt, zal de minimale voorraadbehoefte dus 2% van het totale aantal eenheden bedragen:
Minimale voorraad = (80.000/250) x 7 = 320 x 7 = 2.240 schroeven
We berekenen de veiligheids- of buffervoorraad voor het magazijn. Indien de maximale leveringstermijn van een leverancier in uitzonderlijke omstandigheden 21 dagen bedraagt, dan betekent dit dat de veiligheidsvoorraad 4480 eenheden moet bedragen:
Buffervoorraad of veiligheidsvoorraad = (21-7) x 320 = 4.480 schroeven
Daardoor is de optimale voorraad 24.608 schroeven, oftewel het totaal van het maximale aantal te bestellen schroeven (17.888), het minimale aantal te bestellen schroeven (2.240) en de veiligheidsvoorraad (4.480):
Optimale voorraad = 17.888 + 2.240 + 4.480 = 24.608 schroeven.
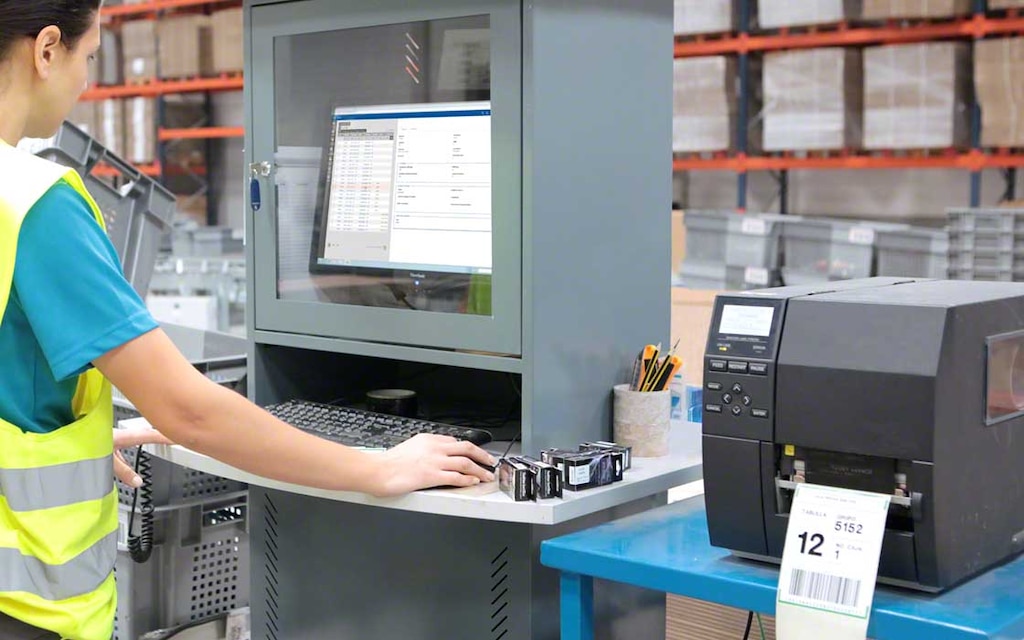
Digitalisering van de optimale voorraad
De digitalisering van de logistieke processen, heeft het mogelijk gemaakt talrijke taken te automatiseren die enkele jaren geleden nog een bron van vergissingen waren, en tijdverlies opleverden voor de magazijnmedewerkers. De implementatie van een ERP (Enterprise Resource Planning) is onder andere van groot belang voor een geïntegreerd beheer van de bestellingen, zodat de vraag naar elk product en de doorlooptijd van elke leverancier bekend zijn. Kortom, het helpt de logistiek manager om de optimale voorraad en het optimale bestelvolume per leverancier te berekenen.
Zodra de optimale voorraad voor elk artikel is berekend, kan een warehouse management systeem (WMS) automatisch prioriteiten stellen bij bepaalde processen, zoals het aanvullen van de orderpickzones, de ontvangst van binnenkomende bestellingen, of het beheer van de productielijnen van de fabriek.
Bovendien bepalen deze toepassingen de optimale voorraad voor elk van de artikelen, waardoor automatisch aanvullingsopdrachten worden gecreëerd voor de referenties, waarvan de voorraad onder het vooraf ingestelde minimum ligt. Een WMS bepaalt automatisch de opslaglocatie van de producten in het magazijn op basis van hun karakteristieken, zoals de omloopsnelheid, de partij of de vervaldatum, waardoor vergissingen worden beperkt en de productiviteit van de installatie wordt verbeterd.
Nauwkeurigheid en flexibiliteit: de essentie van logistiek 4.0
In een steeds veeleisender logistieke en industriële omgeving worden logistieke managers gedwongen de kosten van opslag- en orderverzamelprocessen te verlagen om concurrerend te blijven. Het gebruik van instrumenten voor de optimalisatie van de voorraad, voorkomt vergissingen en extra kosten, door ervoor te zorgen dat er altijd voldoende voorraad is om aan de vraag voor elke referentie te voldoen, zonder dat dit extra uitgaven tot gevolg heeft.
Meer en meer magazijnmanagers introduceren echter oplossingen om de goederenstromen te automatiseren. Zodra het optimale voorraadniveau is berekend, kan een WMS in combinatie met een ERP worden gebruikt om bestellingen bij leveranciers in te plannen en aanvullingstaken te coördineren met betrekking tot de opslaglocaties, naast nog andere geavanceerde functies.
Mecalux levert Easy WMS, een warehouse management systeem met meerdere logistieke toepassingen. Wilt u de efficiëntie van uw bedrijfsprocessen verbeteren en de voorraden perfect beheren? Neem contact met ons op voor meer informatie. Een expert zal u graag adviseren met betrekking tot de beste digitale oplossing voor uw bedrijf.